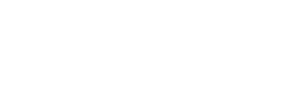
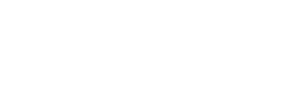
- 713.590.1312
- sale@pandbtools.com
What is a Flanged Gate Valve and Why It’s the Best Choice for Your Industrial Needs?
In the world of industrial machinery, choosing the right components can significantly impact efficiency and safety. One such essential component is the Flanged Gate Valve, known for its robustness and reliable performance in controlling fluid flow. This type of valve is designed with flanges that allow for easy installation and maintenance, making it a preferred choice in various applications across industries. With the ability to handle high pressures and temperatures, a Flanged Gate Valve ensures a tight seal and minimal leakage, which is crucial for maintaining operational integrity. Its popularity in global manufacturing, particularly in leading factories known for their export excellence, underscores its effectiveness and durability. In this blog, we will explore the benefits of Flanged Gate Valves, discuss their design intricacies, and explain why they stand out as the optimal choice for your industrial needs.
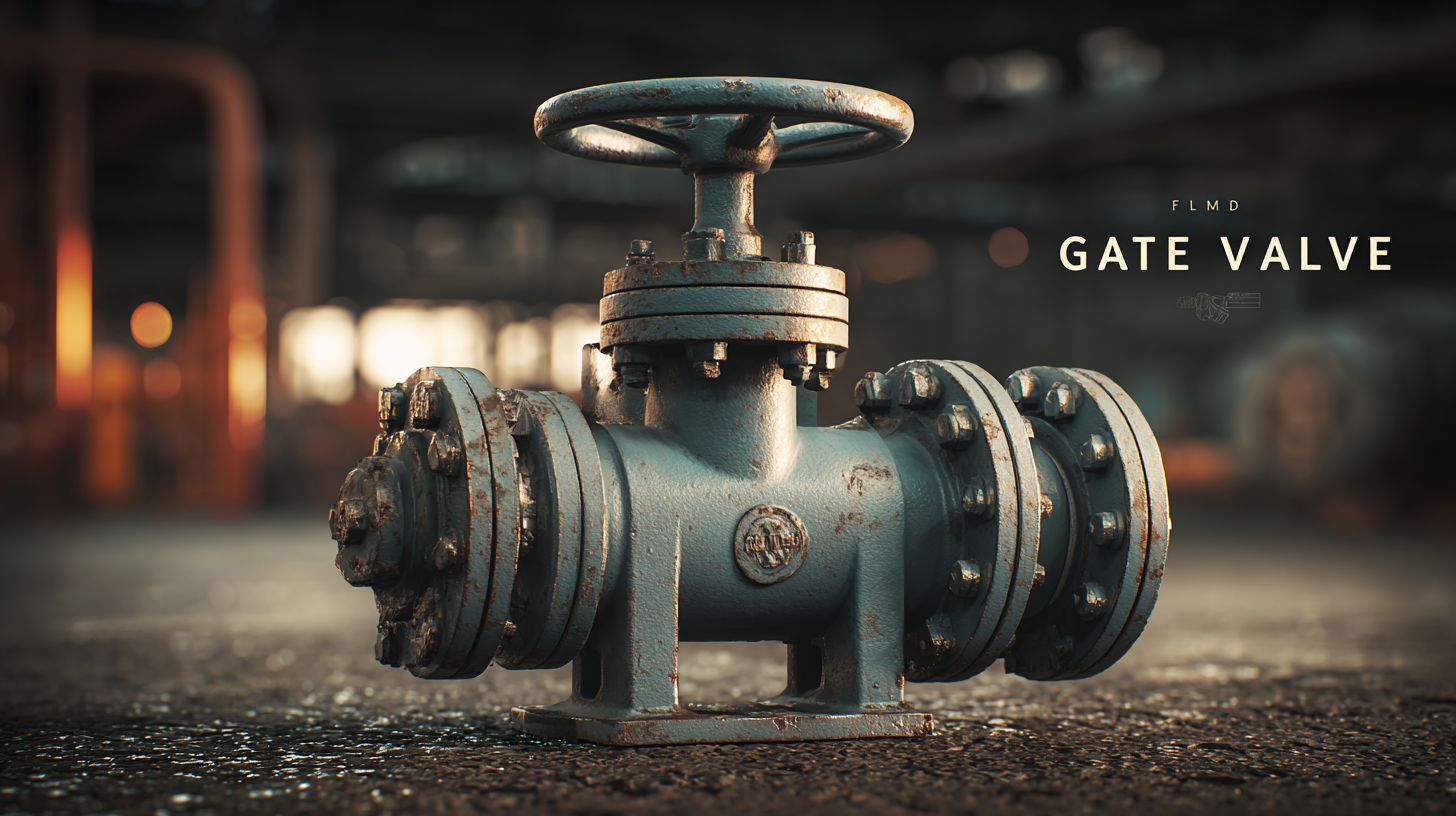
Understanding Flanged Gate Valves: Design and Functionality Explained
Flanged gate valves are essential components in various industrial applications due to their robust design and reliable functionality. These valves are specifically engineered to provide a tight seal when fully closed, which is crucial in minimizing leakage and ensuring efficient fluid control. The flanged design allows for easy installation and maintenance, making them suitable for a range of connection types, including push-on, flange x flange, and mechanical joints. This versatility ensures that flanged gate valves can be effectively used in diverse environments, addressing the unique demands of industrial operations.
Understanding the functionality of flanged gate valves highlights their advantages over other valve types. Their design allows them to handle high pressures and flow rates while maintaining structural integrity. Additionally, innovations in materials, such as stainless steel bodies for high vacuum gate valves, further enhance performance in extreme conditions. As the gate valve market projected revenue increases from USD 12.9 billion in 2018 to USD 14.8 billion in 2023, the growing demand for these valves underscores their significance in industrial processes. Emphasizing both functionality and adaptability, flanged gate valves continue to be a preferred choice for industries aiming for operational efficiency and reliability.
Key Advantages of Flanged Gate Valves for Industrial Applications
Flanged gate valves have emerged as a crucial component in industrial fluid control systems, offering a blend of reliability and efficiency. According to the latest market forecast, the demand for gate valves is projected to grow significantly from 2023 to 2033 as industries seek to optimize their operations. These valves are designed to provide a tight seal, ensuring minimal leakage and energy loss—key advantages in sectors such as oil and gas, water treatment, and chemical processing.
One of the primary reasons for the rising preference for flanged gate valves is their simple yet effective design, which facilitates smooth fluid flow. Unlike other valve types, flanged gate valves are less likely to corrode and are ideal for handling aggressive fluids. Recent industry reports emphasize that the durability and performance of these valves have made them a top choice for new installations and system upgrades, with a projected market growth rate exceeding 6% annually. Additionally, their ease of maintenance contributes to reduced downtime, further underscoring their value in industrial applications.
How to Choose the Right Flanged Gate Valve for Your System
When selecting the right flanged gate valve for your system, understanding the specifics of your application is crucial. Flanged gate valves are characterized by their robust design and ability to provide a tight seal, making them ideal for high-pressure and high-temperature applications. According to a report by MarketsandMarkets, the global industrial valve market is projected to reach $85.2 billion by 2025, with gate valves playing a significant role due to their reliability and efficiency in controlling flow.
When choosing a flanged gate valve, consider factors such as material compatibility, size, and pressure rating. The American Society of Mechanical Engineers (ASME) provides guidelines on the appropriate selection of valve materials based on factors like fluid properties and operating conditions. For instance, stainless steel valves often offer superior resistance to corrosion, making them suitable for chemical and oil applications, whereas cast iron valves might be sufficient for water systems. Ensure that the selected valve complies with industry standards, such as API 600, to guarantee optimal performance and safety in your industrial applications.
What is a Flanged Gate Valve and Why It’s the Best Choice for Your Industrial Needs? - How to Choose the Right Flanged Gate Valve for Your System
Feature | Description | Benefits |
---|---|---|
Material | Various options including cast iron, stainless steel, and bronze | Long-lasting durability and corrosion resistance |
Pressure Rating | Available in ANSI classes 150 to 2500 | Suitable for high-pressure applications |
Size Range | Available in sizes from 1 inch to 48 inches | Flexibility for various pipe diameters in industrial systems |
Operation | Manual or powered operation options | Easier control and operation efficiency |
Sealing Type | Rising and non-rising stem configurations | Optimal sealing performance in different installations |
Applications | Water, oil, gas, and other industrial fluids | Versatile usage across multiple sectors |
Installation and Maintenance Tips for Optimal Performance
Flanged gate valves are essential components in many industrial applications, offering durability and reliability. However, ensuring optimal performance involves careful installation and regular maintenance. To start, it’s crucial to install flanged gate valves in accordance with the manufacturer's specifications. Using appropriate gaskets and ensuring proper alignment can prevent leaks and extend the life of the valve.
Maintenance is equally important. Regularly inspecting for signs of wear and lubricating moving parts can significantly enhance performance. For instance, utilizing the right lubricant not only reduces friction but also prevents corrosion, which is vital in maintaining the integrity of the valve. Additionally, operators should monitor the valve’s operation to identify any irregularities early, thereby avoiding costly downtime. Properly planned maintenance schedules can lead to improved efficiency and productivity, reflecting the current trends in the industrial sector toward automation and enhanced machinery performance.
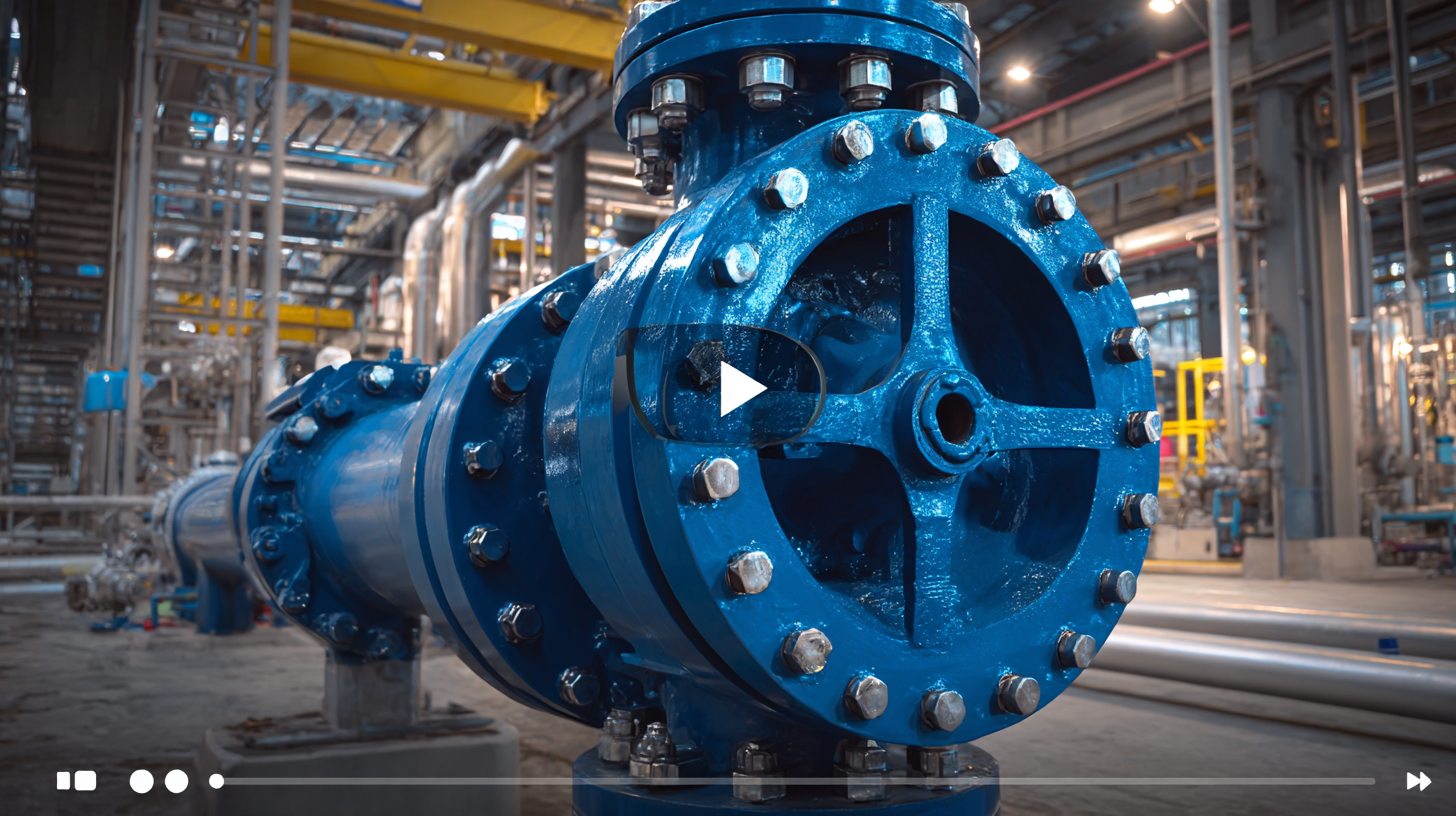
Common Applications of Flanged Gate Valves in Various Industries
Flanged gate valves are widely utilized in various industrial applications due to their robust design and reliable performance. One of the most common uses is in water and wastewater treatment plants, where they regulate and isolate flow in large pipelines. The flanged connection allows for easy installation and maintenance, making it ideal for environments where access may be limited. These valves excel in controlling high-pressure systems, ensuring a tight seal to prevent leaks and maintain operational efficiency.
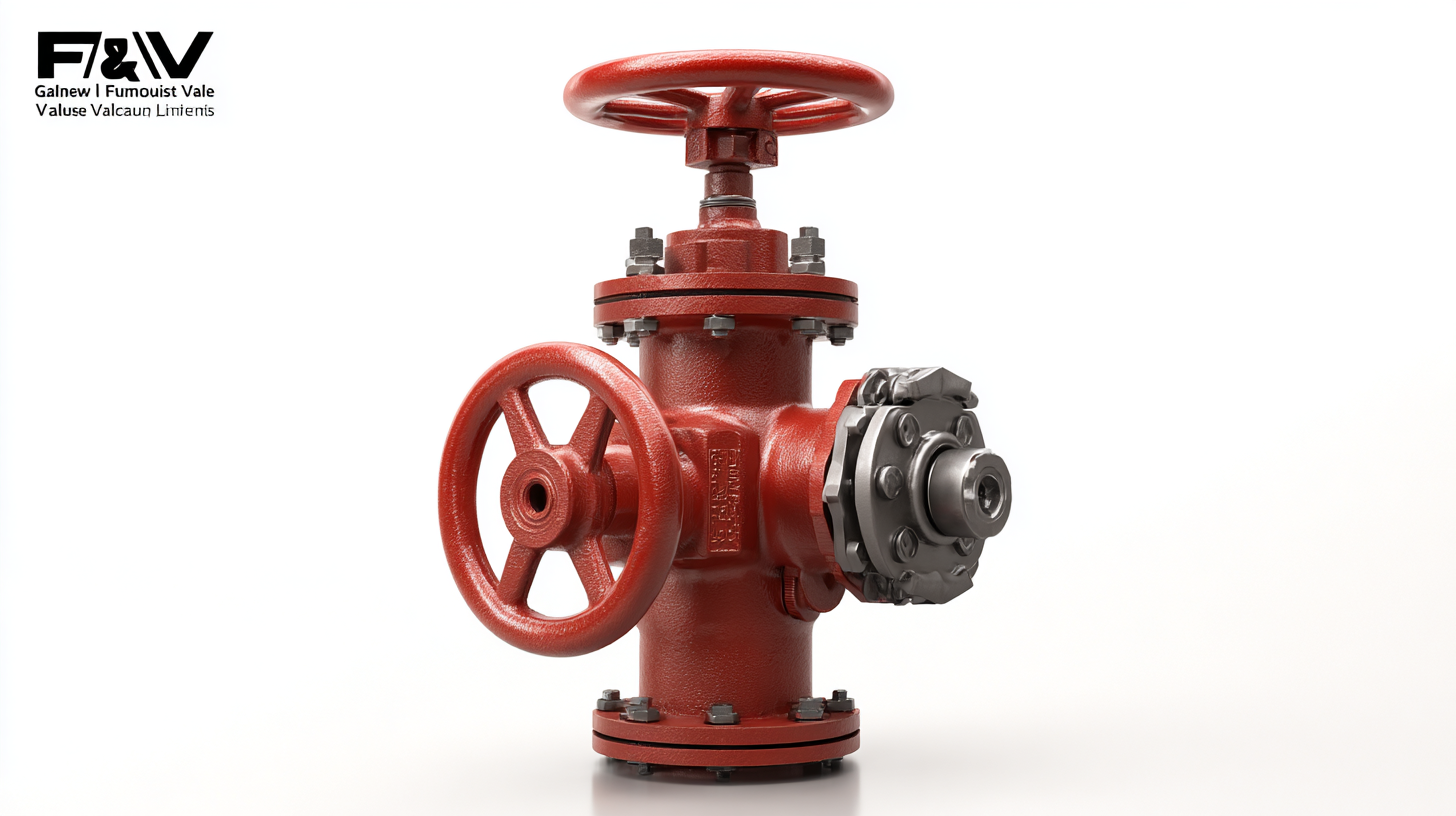
In the oil and gas industry, flanged gate valves are essential for onshore and offshore installations. They are frequently found in pipeline systems that transport crude oil, natural gas, and refined products. Their ability to handle high temperatures and pressures, combined with their durable construction, makes them a preferred choice for managing the safety and integrity of critical operations. In addition, flanged gate valves are also commonly used in chemical processing facilities, where they assist in managing the flow of corrosive substances while minimizing the risk of spills and environmental hazards.